PART THREE:
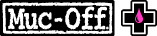

PART THREE:
A bicycle lubricant’s chemistry is of fundamental importance to its ability to reduce friction or wear. Whether formulated for performance or durability, the blend of base oils and additives defines how well a lubricant will perform its task.
A world of complexity lies beneath a lubricant’s surface. The interaction of chemical components takes place at the molecular level in a world invisible to the human eye. The relationships they share, their capacity to work together (“synergistic”) or to nullify the other’s effect (“antagonistic”) are among the numerous factors considered by Muc-Off’s scientists.
Absorbency, viscosity, lubricity, solubility and even volatility: these and countless other considerations are the sphere of the industrial chemist. Temperature and pressure, speed and load, hardness and surface finish feature among a host of factors that can affect lubricant performance, whether blended for performance or durability.
Our research with the Laboratory of the Government Chemist (LGC) and the National Physical Laboratory (NPL) has been instrumental in developing a new protocol to identify the most widely used chemical components in a process achieved with Gas Chromatography Mass Spectrometry (GC/MS) and Atmospheric Solids Analysis Probe Mass Spectrometry (ASAP-MS).
The process of creating a new lubricant is time-consuming. Individual additives must be selected and tested to see not only how they work by themselves, but within the formula. Every single amendment has to be tested multiple times, the data is then analysed, and a decision is made on what to try next. The R&D team have to reformat the dyno every single time an ingredient changes. It's a painstaking process, but one that gives the most complete results and ultimately, the best lubricant possible.
During the development of a chain lube there are a number of decisions that need to be made regarding the final formulation. It is important to understand that a formulation can have as few, or as many individual components, depending on the requirements of the lube. As an example, say you want to formulate a chain lube that is both efficient and has good durability. First, you would want to determine what type of lube would it be; water-based or oil-based. Regardless of the type of lube decided upon, there will be a wide range of base fluids that can be selected.
Given that efficiency and durability are the performance requirements from the lube, the key properties that the lube must have, are good wear properties and low friction. To achieve this, you would need to select the chemicals (additives) that will be responsible for enhancing the friction and wear properties. In essence, you would have to select suitable friction modifiers (for low friction) and anti-wear additives (for low wear). In this scenario, you can use one type of friction modifier or a combination of two or more. The same can be said of the anti-wear additives.
In addition to selecting the type of additives to use, another decision must be made with regards to the concentration of the individual additives in the formulation. If by good fortune, the formulator manages to determine the combination of the additive with their optimum concentrations, the formulator has the additional challenge of the aesthetics of the lube. This includes things such as colour and fragrance, which can in some instances, be a necessity; in order to mask any strong odour of the additive or base oil mixture.
All lubricants are made up of a base oil and additives. Sometimes, more than one base oil is used. The base oil always takes up the greater part of a lubricant. The pool of base oils which our chemists can choose is broad. Selection is always critical and heavily dependent on experience.
A base oil’s relationship to additives is also defined by purpose. While the base oil carries the burden of lubricating the chain, additives perform specific functions. There is no theoretical method of calculating the correct proportion of base oil and additive. The chemist’s experience is critical. For the less experienced, the presence of sediment – undissolved additive – is an unmistakable sign of proportional imbalance.
It’s possible of course to reverse the proportion of base oil and additive and to formulate a lubricant entirely from additive. The truth of a lubricant’s performance, however, lies in its blend as much as in its components.
A performance lubricant reduces friction. Its ability to do so depends upon the careful selection of cutting-edge chemical components. Friction modifiers are many and varied, but the main categories include organic friction modifiers, polymeric friction modifiers, micro-nano particles and organo-molybdenum friction modifiers. Organic friction modifiers are typically created from oleic acid, oleyl amide or stearic acid, but there are more varieties. These friction modifiers (chemical compounds) consist of a polar head and non-polar tail. The polar heads are attracted to the reactive rubbing surfaces leaving. The non-polar tails spread outwards from both surfaces forming a low-friction shear plane where they meet each other. This low friction shear plane is responsible for friction reduction.
Polymer friction modifiers can contain an alkyl methacrylate compound. Their function and behaviour serve the same purpose in a bicycle lubricant as an organic friction modifier: polar heads attach to the surface of the lubricant to form a low friction shear plane.
Nanoparticles, or ‘micro-particles’, are more complex. Their behaviour varies with type. Some form low-friction shear planes like those previously described, while others, such as PTFE, have intrinsic friction-reducing properties derived from their ability to ‘roll’ within contacts. All nanoparticles share an insoluble property which means that they compact, rather than dissolve in the lubricant, or sediment depending on the density and rise to the lubricant’s surface.
Polymer Friction Modifier Diagram
A lubricant formulated to boost durability does so by reducing wear. Tribofilms are only one method, and these are formed due to the presence of anti-wear additives. A further method exists by creating formulas with additives of high molecular weight. These ‘long chain’ components form fibre-like structures that create a ‘second surface’, separating the drivetrain’s contact areas by only a few microns. Reduced contact, naturally, means reduced wear.
Our ability to now determine the chemical components of leading lubricants is one of the most significant achievements of our research project with LGC and NPL - it is innovation at its finest. The processes used to reverse engineer a chemical formula were Gas Chromatography Mass Spectrometry (GC/MS) and Atmospheric Solids Analysis Probe Mass Spectrometry (ASAP-MS).
As suggested by the name, Gas Chromatography Mass Spectrometry (GC/MS) works by measuring the lubricant’s behaviour when heated to its boiling point. It is first mixed with a solvent and injected into the chromatography column of a highly sophisticated analytical machine, which also contains gas, oxygen or an ‘enactor’ such as argon or helium. Introducing the sample to the column pushes out the gas.
Atmospheric Solids Analysis Probe Mass Spectrometry (ASAP-MS) is similar to the gas chromatography analysis described above but conducted at higher temperatures and used when analysis by gas chromatography has failed to identify certain chemical components. Both provide a spectra for analysis.
But we do not have a continuing need to reverse engineer our competitors’ products. Having established the most commonly used chemical components, we can add to our test literature and accelerate the development of our own formulas.
The scope of the lubricant category is huge. Few others help the rider to overcome such a wide range of challenges. Most bicycle products only solve one problem. Chain lubricant can be an aid to performance, durability and protection, depending on the formula.
But some challenges cannot be overcome by a lubricant. Poor maintenance routines, mechanical inefficiencies and climatic conditions which the lubricant is not optimised for will defeat even the most advanced formula. Choose your lubricant carefully and use it as part of a regular and comprehensive maintenance routine for the best performance.
Do you want to shop on our UK site?
Do you want to shop on the EU site?
Do you want to shop on the US site?